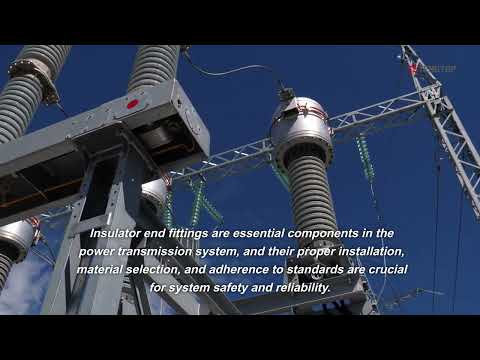
Insulators are essential components in high-voltage power transmission systems as they play an important role in keeping the electrical current flowing safely. Composite insulators, also known as non-ceramic or polymer insulators, have become more popular because of their better performance and longevity. Insulator end fittings are vital components that connect the insulator to the conductor or other components in a transmission line. In this blog post, we will explore the importance of insulator end fittings, the different types available, installation techniques, materials used in their construction, and relevant standards.
The Role of End Fittings in Composite Insulators:
End fittings are crucial components for composite insulator installation and connection. They secure the insulator to the structure and prevent it from breaking away from the conductor. End fittings also provide a reliable mechanical interface between the insulator and the structure, ensuring that the insulator’s load-carrying capacity is not compromised. They are also responsible for transferring the tensile and compressive loads from the insulator to the tower or pole and absorbing any bending moments.
Types of End Fittings: A Comprehensive Overview:
There are several types of insulator end fittings available, depending on their application and structure type. The most common ones include ball-and-socket, tongue-and-clevis, socket-eye, and yoke fittings.
Ball-and-socket fittings consist of a ball-socket coupling that allows for angular movement along a radial plane, making them ideal for areas with high wind loads. Tongue-and-clevis fittings offer similar angular movements but with less resistance to axial loads. They are the most commonly used fitting in overhead transmission lines. Socket-eye fittings provide a secure straight-line pull and are typically used where the insulator axis needs to be in line with the conductor axis, while yoke fittings are for use when the conductor needs to be held in a fixed position.
Installation Techniques for Insulator End Fittings:
End fittings can be installed using different techniques, depending on the operational circumstances and the design requirements. One of the most common methods is the crimping technique, where end fittings are attached to insulators using a specific crimping tool. Another technique is the mechanically lined technique, which involves permanently attaching the metal end fitting to the insulator using epoxy glue. The injection molding technique involves injecting the polymer material into the metal end fitting, allowing for a strong bond between the two materials.
Material Selection for Durable Insulator End Fittings:
The choice of material for insulator end fittings plays a critical role in their longevity and durability. The most commonly used materials are aluminum, steel, and composite materials. For ball-and-socket fittings, aluminum is a popular choice because of its high strength-to-weight ratio and corrosion resistance. For tongue-and-clevis fittings, steel is typically used because of its high strength and rigidity. For socket-eye fittings, both steel and aluminum are commonly used, while composite materials are used for yoke fittings because of their excellent insulation and corrosion-resistant properties.
Standards and Regulations Governing Insulator End Fittings:
To ensure the safety and reliability of power transmission systems, several standards have been established to regulate the design, testing, and manufacture of insulator end fittings. Some of these standards include IEC, ANSI, and GB standards, which cover critical aspects such as mechanical strength, electrical properties, and environmental performance. Additionally, regulatory bodies, such as the National Electric Safety Code (NESC) and the Occupational Safety and Health Administration (OSHA), have also established guidelines to govern the safe operation and maintenance of transmission lines.
Insulator end fittings are essential components in the power transmission system, and their proper installation, material selection, and adherence to standards are crucial for system safety and reliability. Understanding the different types of end fittings available, installation techniques, materials, and standards can help system operators and designers make informed decisions when selecting and installing insulator end fittings. They also play a critical role in the system’s overall sustainability by ensuring that power is delivered safely and efficiently.